
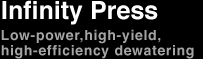
Basic performance
Air spring adopted in cylinder press
By adopting an air spring in the cylinder press, highly efficient and stable dewatering is performed by the compressor which transmits power extremely efficiently by building pressure at an angle of 45°

Unique design punched plate dimensions gives longer operating life
By adopting comparatively small holes (φ 16 mm) in the drum-shaped punched plate which is at the heart of this machine, the problem of mesh tear due to overloading has been reduced thereby achieving a longer operating life of the wire mesh. A sufficiently thick punched plate has also been adopted.

Stock material clogging avoided
By doing away with vat shapes that can cause problems of stock material clogging (Seckle method ) and adopting a deeper vat profile to eradicate the buildup of large pockets of abnormal high-density stock material, overcurrent tripping caused by stock material jamming has been eliminated. The issuance of stock material from inside the vat is improved which also counters any problems after prolonged periods of downtime.

Stock material clogging avoided
By doing away with vat shapes that can cause problems of stock material clogging (Seckle method ) and adopting a deeper vat profile to eradicate the buildup of large pockets of abnormal high-density stock material, overcurrent tripping caused by stock material jamming has been eliminated. The issuance of stock material from inside the vat is improved which also counters any problems after prolonged periods of downtime.

Dewatering efficiency streamlining method
Dewatering efficiency increased by dewatering at the stock material injection stage
In the past, stock material has been almost entirely fed from the bottom. However, this machine has been designed so that the stock material is injected from above so that when it overflows from the headbox it pours directly onto the wire mesh thereby generating a dewatering force as the stock material strikes the wire mesh. By adopting this method, dewatering at the time of injection is momentarily intensified; therefore, a greater dewatering force is achievable. In addition, the machine is made more compact and is capable of even higher intensity dewatering. Furthermore, since the stock material injection status can be checked visually, any injected stock material concentration errors can be immediately observed.

Low filtrate concentration
This machine's dewatering technique creates a thick mat. The concentration of the wastewater filtrate is remarkably low by comparison to other dewatering machines, producing an excellent percentage yield. Due to the excellent extraction rate, the minimum required supply pump can be used to save energy and there is no need to consider recovering raw material from the filtrate.

Drive power
This machine is designed so that all drive units in the machine are driven directly thereby reducing loss of transmission to an extreme minimum, which enables the machine to operate by the minimum power requirement. At the same time, because it is directly driven by hollow-shaft geared motors without utilizing axis couplings and transmission gear drives, fewer components are used thereby creating a substantial cost reduction.
|